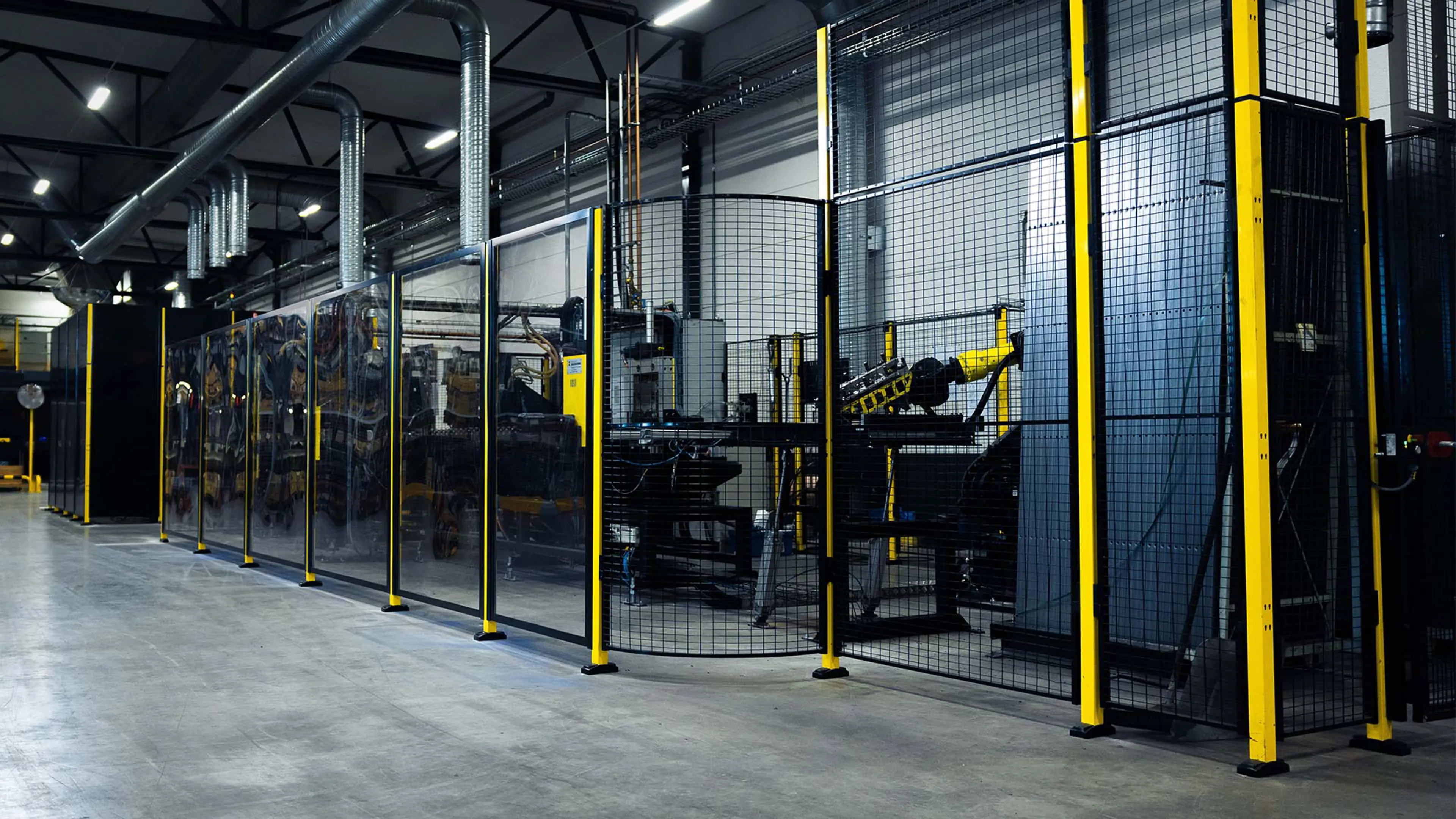
3.0
Machine Safety
To make it easier to access important safety standards for machinery, the following sections provide key rules from these standards, along with straightforward illustrations.
Basic rules
Risk assessment - Why and how?
Often, the primary focus when designing a machine is function, efficiency, and financial concerns. Safety is often overlooked, especially in the early stages of a project. For more in-depth information about how and why a risk assessment is conducted go to chapter 2.1 “Risk assessment”.
Conducting risk assessment early improves machine safety
It can be very difficult to integrate safe operation into the overall functional and operating concept later on.
In fact, safety measures added during the final stages of the project often impair operation and efficiency. It is better to think about potential hazards from the beginning and start thinking of solutions as early as possible.
This process of identifying hazards, determining their risk potential and then reducing or eliminating such risks is referred to as “risk assessment”.
The basic steps are:
- Eliminate the hazard, if possible.
- If you cannot eliminate the hazard, lock the hazard in or lock the people out.
- If you cannot keep people out, monitor their presence near the hazard to stop it in time.
This process of identifying hazards, determining their risk potential and then reducing or eliminating such risks is referred to as “risk assessment”.
In the past, engineers normally did not follow a methodical approach to safety issues. Since stricter regulations and standards on product safety were introduced during the 1990s, “risk assessment” has become the most important step towards safe products and conformity with regulations.
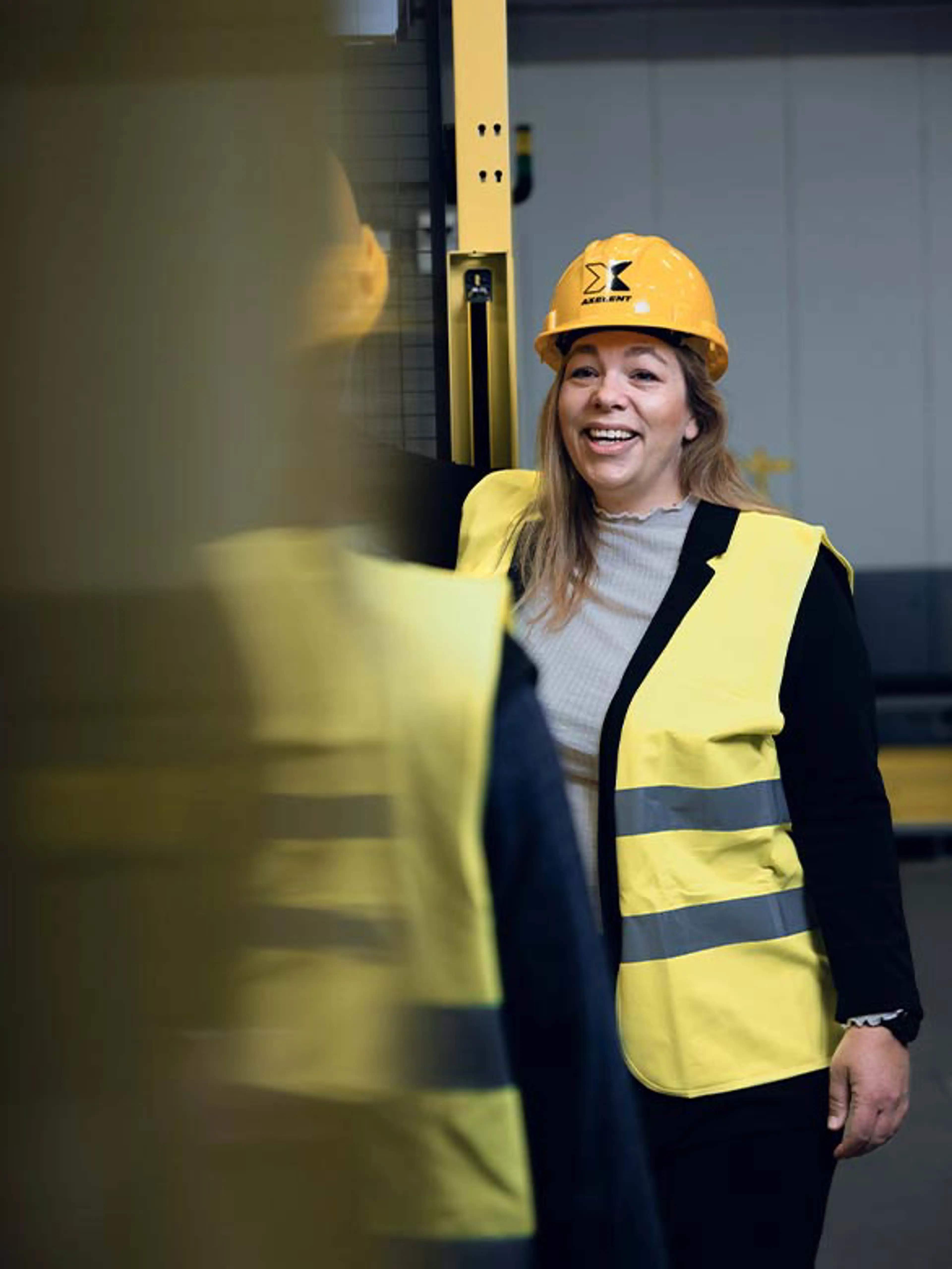
Five steps to conduct a risk assessment
Most regulations and standards on the subject require five steps to be taken in risk assessment.
- Determine the limits of the machinery, including the intended use and potential misuse.
- Identify the hazards generated and the associated hazardous situation.
- Estimate the risks, considering the severity of possible injuries and the probability of their occurrence.
- Evaluate the risks and determine whether risk reduction is required.
- Eliminate the hazards or reduce the risk associated with these hazards by applying protective measures
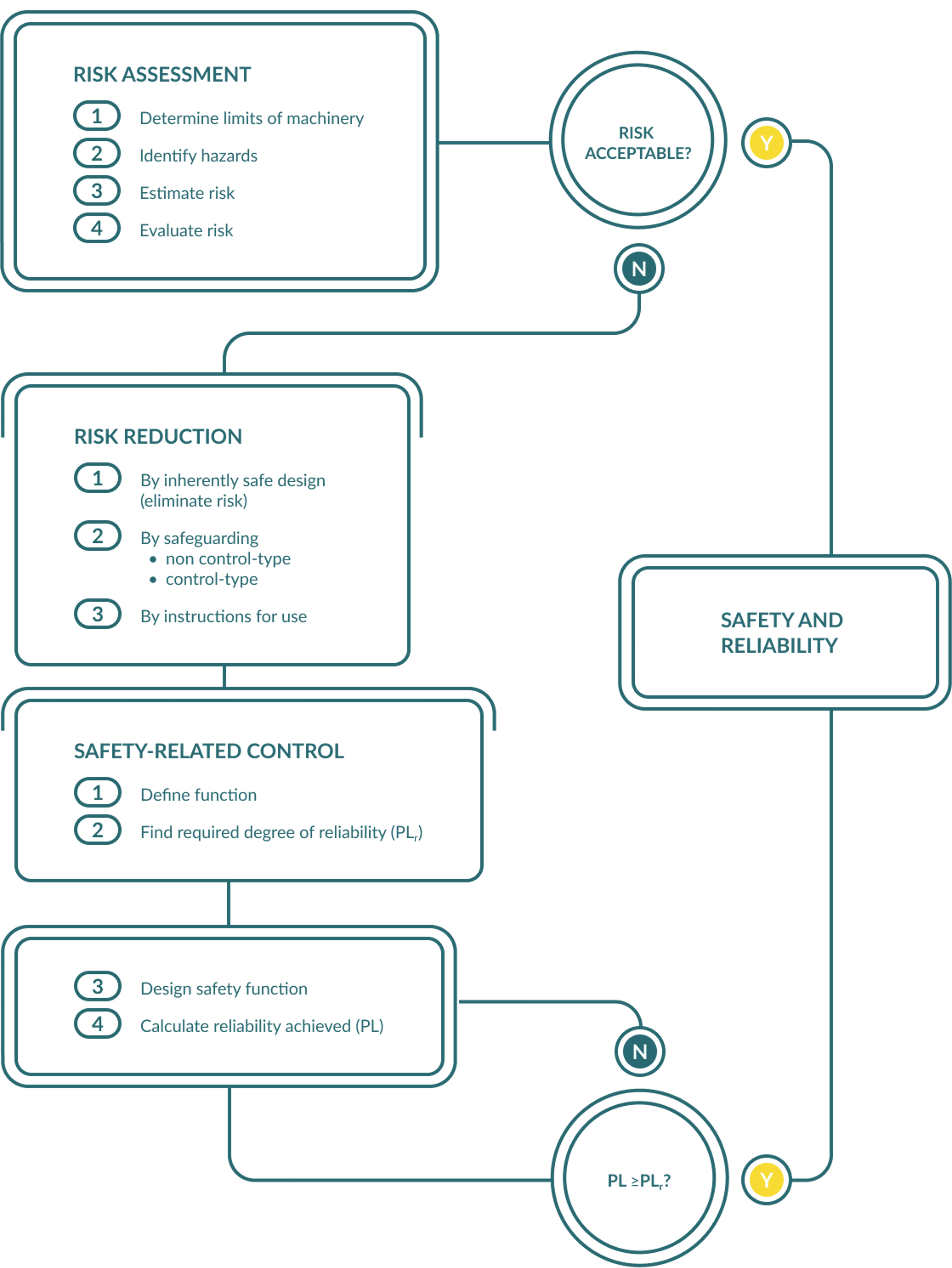
Overview of each step in risk assessment
Understanding and implementing a thorough risk assessment process is crucial for ensuring machinery safety and reliability. Below is a detailed breakdown of each step:
Follow a life risk assessment now
Define task to be assessed
Task:
Operator brings pallet into the machine and checks it.
Find the hazards and describe the hazardous event
Hazard
Approach of a moving element to a fixed part:
- Crushing, shearing
- Impact
Hazardous event
Operator may be crushed between moving robot and pallet or machine parts.
Select a safety measure
Type of measure:
Combination of guards and protective devices (llc).
- The hazard zone is enclosed by a guard fence that prevents intentional and unintentional access.
- A door is provided for access, which serves as a movable guard.
- The movable guard is provided with interlocking and guard locking that holds the door closed until robot and machine movements in the hazard zone have stopped.
- The machine cannot start as long as the door is still open or not locked.
- The door switch must be provided with an escape release lock.
Allocate requirements from directives/standards
Machinery directive:
- 1.3.7 – Risk related to moving parts
- 1.4.2.1 – Fixed guards
- 1.4.2.2 – Interlocking movable guards
EN ISO 12100: 2010: sections 6.3.3.2.2 and 6.3.3.2.3
Do a risk estimation to find the PL for the interlocking function
Do a risk estimation to find the PL for the interlocking function
S – Severity of injury: 2
Operator could be seriously injured by the robot, fatal injury possible.
F – Frequency and duration: 1
The pallet must be replaced approximately once per hour.
P – Prevention of harm: 2
The robot moves at speeds of up to 10 m/s, avoidance hardly possible.
O – Probability of occurrence: 2
No evidence available.
PLr: d